Cleaning Equipment for Filtration Elements
Cleaning Equipment
After a period of use, the filtration elements may be blocked by dirt substance. Therefore, before using it again, the filter elements need to be cleaned.
1. Removal of impurities: The filter element will accumulate impurities during use, such as particulate matter, sediment, organic matter, etc. These impurities will reduce the filtering effect and affect the performance of the equipment. Cleaning the filter element can effectively remove these impurities and maintain the normal operation of the filter element.
2. Restoring Permeability: Over time, filter elements may become less permeable, resulting in less effective filtration. Cleaning can help restore filter element permeability and improve filtration efficiency.
3. Prevent the growth of bacteria: The filter element, as a device for separating impurities, is prone to the growth of bacteria and microorganisms. Cleaning the filter element can remove these bacteria and ensure the hygienic safety of the product.
4. Extended service life: Frequent cleaning of filter elements can extend their service life and avoid the need to replace elements due to clogging or damage.
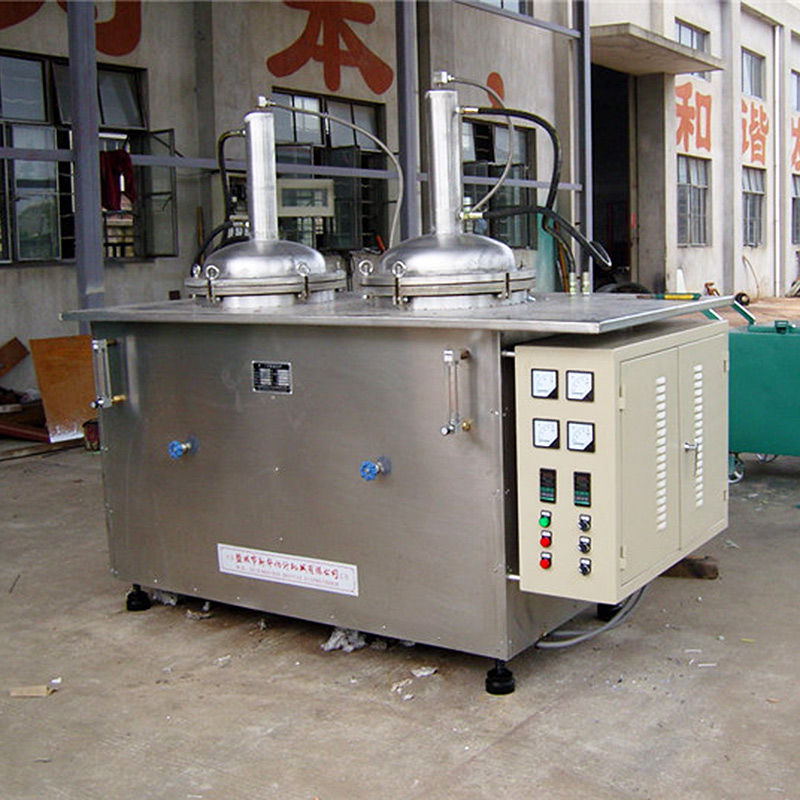
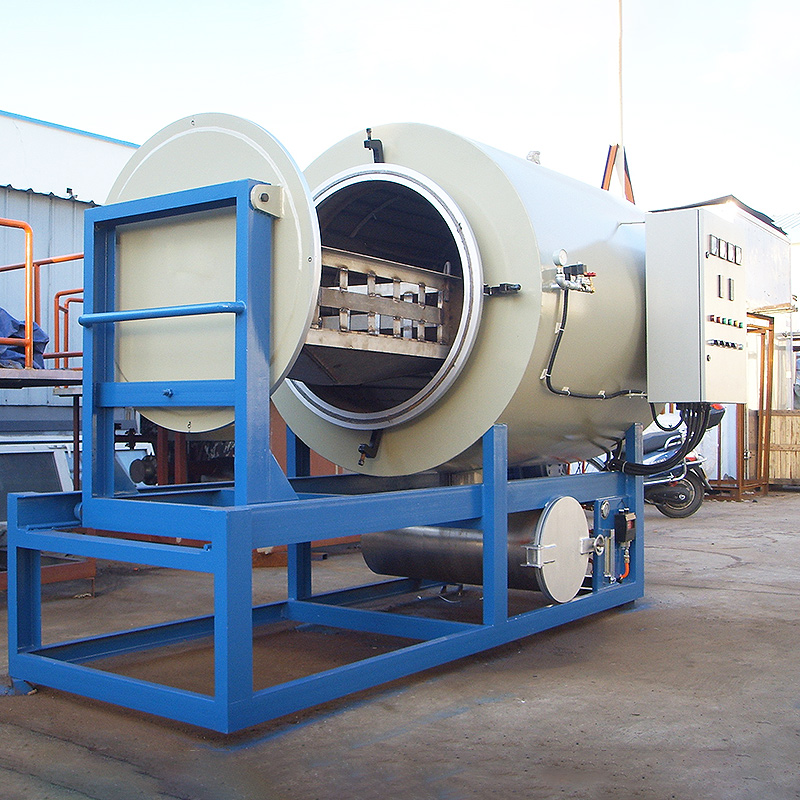
To sum up, filter element cleaning is an important step to ensure the filtering effect and equipment performance, which helps to maintain the normal operation of the filter element and prolong its service life.
In the industry of polymer application, cleaning is mainly done using physical and chemical methods to remove the adhered melt polymer through high-temperature calcinations, dissolution, oxidation, or hydrolysis, followed by water washing, alkaline washing, acid washing, and ultrasonic cleaning. Accordingly we can provide the cleaning equipment, such as Hydrolysis cleaning system, Vacuum cleaning furnace, TEG cleaning furnace, Ultrasonic cleaner and some auxiliary device, such as alkali cleaning tank, washing cleaning tank, bubble tester.
Hydrolysis cleaning system refers to a cleaning process that utilizes the chemical reaction of hydrolysis to break down & remove polymer from surfaces or equipment. This system is commonly used in industrial settings, such as in the cleaning of heat exchangers, boilers, condensers, filtration elements and other equipment that may accumulate deposits.
The principle of Vacuum cleaning furnace is based on the property that high molecule of synthetic fiber, isolated from air, is to be molten when the temperature reaches up to 300˚C, then melt polymers flow into waste collecting tank; when the temperature increases to 350˚C, up to 500˚C, polymer starts to degrade and exhaust out of furnace.
TEG cleaning furnace: It uses the principle that polyester can be dissolved by glycerol (TEG) at its boiling point (at normal pressure, it is 285°C) to achieve the purpose of cleaning.
Ultrasonic cleaner: it is a device that emits vigorous mechanical vibrations into a liquid bath. This device achieves cleaning purposes through the use of sound waves. The sound waves create cavitations through the movement of the liquid bath, resulting in a detergent effect on the surface of the item being cleaned. It releases energy up to a level of 15,000 psi in order to loosen and eliminate dirt, grime, and impurities.